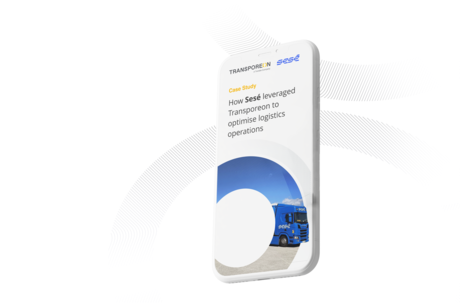
Sesé
About Sesé
Sesé is a global supply chain partner, delivering sustainable, innovative solutions tailored to each customer’s unique needs. With a focus on operational excellence, the company operates a vast fleet serving a broad spectrum of industries. Sesé's commitment to leveraging cutting-edge technology has allowed it to enhance efficiency, reduce operational costs and deliver superior service to its clients.
For years, Sesé has remained at the forefront of industries like automotive, e-commerce, healthcare and more. Managing thousands of transports annually, the company continues to meet the growing demands of its clients while integrating the latest in logistics technology.
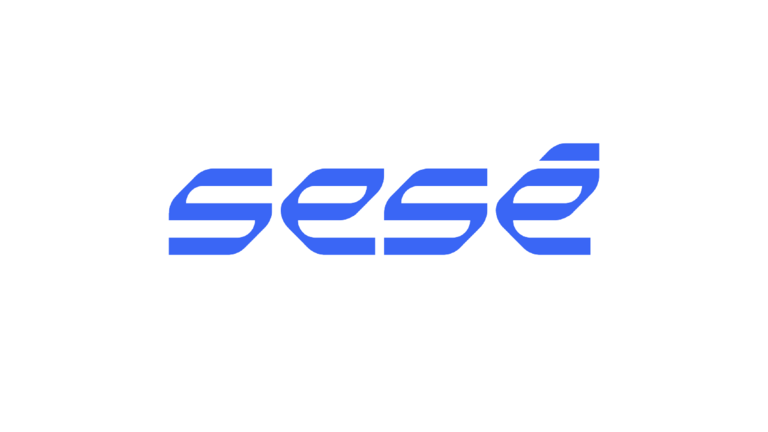
Quick facts about Sesé
Driving logistics innovation globally.
Headquartered in Zaragoza, Spain, Sesé provides top-tier logistics services across a wide range of industries, with an extensive operational reach.
-
Industries served: automotive, e-commerce, healthcare, electric mobility, construction.
-
18 countries throughout Europe, America, Africa and Asia
-
Annual transports: thousands of deliveries across Europe.
-
Fleet: a diverse range of vehicles to meet varying logistical needs.
-
Employees: +14,700 professionals in dedicated team managing operations and logistics solutions.
-
Key solutions: Transporeon Time Slot Management, Real-Time Yard Management, Analytics & KPI Evaluation.
-
Various business divisions: land, air and sea transport; logistics and industrial services.
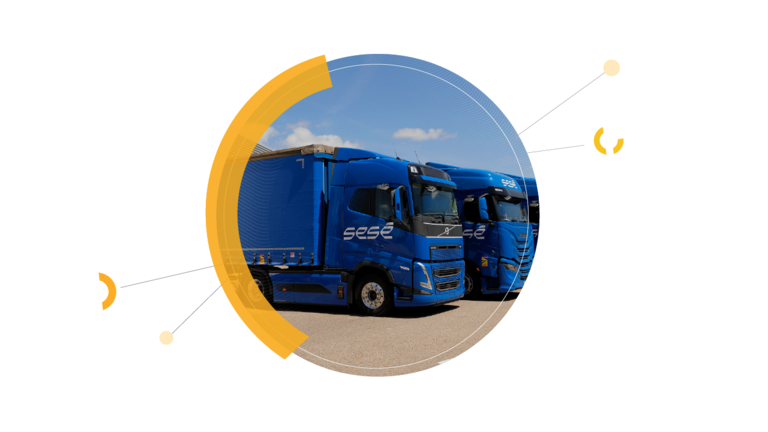
The challenge
Logistical Bottlenecks and Operational Hurdles.
As a forward-thinking logistics leader, Sesé has always prioritised continuous improvement and operational excellence. In its pursuit of smarter, more streamlined processes, the company identified several key areas where enhanced coordination, visibility and data-driven decision-making could unlock even greater efficiency. Opportunities for optimisation included improving scheduling consistency, reducing waiting times at loading and unloading points and enhancing yard management to ensure smoother material flow. Additionally, gaining more precise insights into KPIs such as loading and unloading times was a crucial step towards even more agile, informed logistics operations.
To support this evolution, Sesé turned to Transporeon for a solution that could elevate performance, boost transparency, and future-proof their supply chain capabilities.
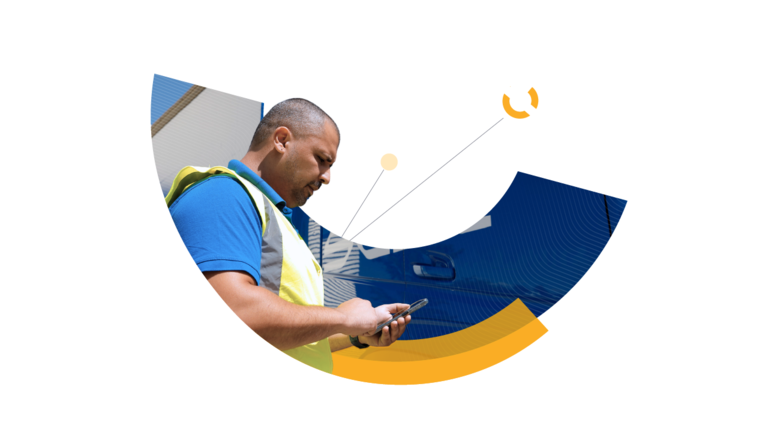
The solution
Sesé turned to Transporeon to streamline its logistics operations, improve coordination and optimise resources. The key solutions were Time Slot Management and Real-Time Yard Management.
Additionally, Analytics and KPI Evaluation provided valuable insights, while the Dashboard feature enabled the quick identification of bottlenecks for data-driven decisions. The seamless integration of Transporeon’s platform into Sesé’s existing systems ensured a smooth, cost-effective implementation. This transformation improved internal processes and communication with stakeholders, creating a more efficient logistics network.
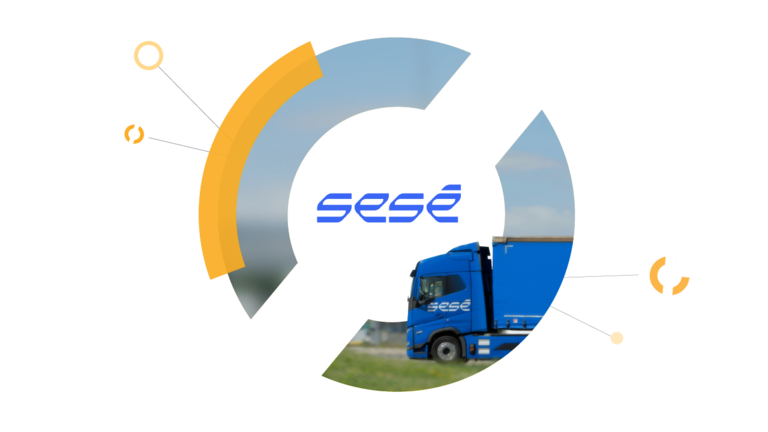
The results
Since implementing Transporeon’s solutions, Sesé has significantly improved operational efficiency by reducing waiting times and downtime costs.
Better scheduling and resource allocation have streamlined internal processes and enhanced yard management.
The use of automated KPI tracking has provided valuable insights for continuous performance improvements. These changes have led to smoother operations and higher customer satisfaction, allowing Sesé to meet demands more efficiently.
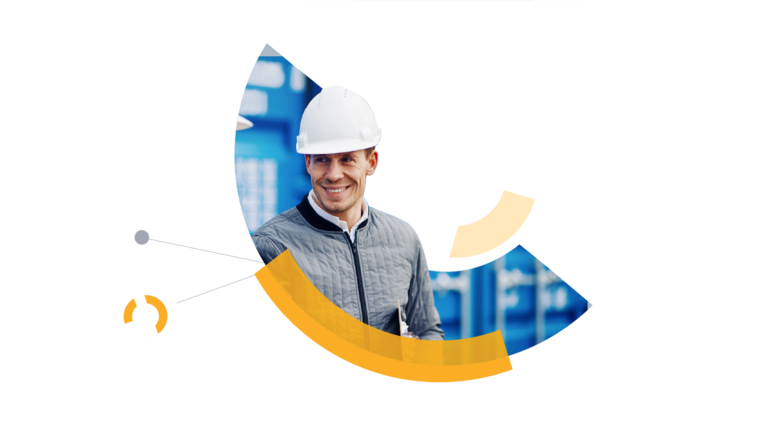